Wer diesen Blog regelmäßig liest, hat es bereits mitbekommen. Die Solarbranche kämpft derzeit mit einem größeren Serienfehler, der zum Versagen der Rückseitenfolien führt. Dabei stellt sich für jeden Betreiber einer Photovoltaikanlage unmittelbar die Frage, welche Rückseitenfolien denn wohl bei seiner eigenen Anlage verbaut sein mögen ? Dass man diese Frage mittlerweile beantworten kann und wie es dazu kam, beschreibe ich in diesem Artikel.
Zunächst ein paar kurze einführende Hinweise zum Thema Rückseitenfolie. Der grundlegende Aufbau eines handelsüblichen Solarmoduls mit kristallinen Solarzellen sieht so aus, dass hinter der Frontglasscheibe zunächst eine Schicht mit EVA Folie kommt, danach folgt dann die Solarzelle. Auf der Rückseite der Zellen kommt dann nochmal eine Schicht EVA und danach kommt die Rückseitenfolie, die ebenfalls wieder aus mehreren Schichten bestehen kann. Ich spreche hier von sogenannten Glas-Folie-Modulen. Bei Glas-Glas Modulen folgt auf die hintere EVA Schicht direkt eine zweite Glasscheibe. Die Solarzellen werden also in ein Sandwich von Kunststofffolien eingebettet, das in der Produktion in einem Ofen zusammenlaminiert wird. Das EVA dient im Wesentlichen dazu, die Solarzellen einzubetten und dafür zu sorgen, dass die unterschiedlichen Ausdehnungskoeffizienten von Glas und Silizium nicht zu mechanischen Spannungen führen. Die wichtigste Eigenschaft des EVA ist dabei, trotz dauerhaftem Beschuss mit UV Strahlung, nicht seine Transparanz zu verlieren und möglichst viel Sonnenstrahlung zu den Solarzellen durchzulassen. Es soll hier noch einmal der Hinweis darauf erfolgen, dass Kunststoffe oft dazu neigen, ihre Eigenschaften unter dauerhafter Einwirkung von kurzwelliger (und damit energiereicher) UV Strahlung zu verändern. Die rückseitige Folie auf einem Solarmodul hat in erster Linie die Aufgabe, die Solarzellen vor Umwelteinflüssen zu schützen. Es soll möglichst kein Wasserdampf in das Laminat eindiffundieren, da Feuchtigkeit zu einer Korrossion der Kontakte zwischen den einzelnen Zellen führen kann. Außerdem muss gewährleistet sein, dass die rückseitigen Folien für eine hohe elektrische Isolation der eingebetteten Zellen sorgen. Immerhin arbeiten moderne PV-Anlagen mittlerweile schon mit Systemspannungen von bis zu 1500V. Bedenkt man, dass heute nahezu ausschließlich trafolose Wechselrichter zum Einsatz kommen, so kann das Berühren einer schadhaften Rückseitenfolie während des Betriebes sehr schnell lebensgefährlich werden. Es ist daher unbedingt notwendig, dass die Isolationsfähigkeit der Rückseitenfolien dauerhaft erhalten bleibt. Um diese Bedingung während der langen Lebenszeit einer PV-Anlage zu gewährleisten, machen die Wechselrichter jeden Morgen vor der Zuschaltung zum Netz eine sogenannte Isolationsprüfung. Zu diesem Zweck werden in aller Regel Prüfspannungen von 1000V bzw. 1500V auf den kurzgeschlossenen Solargenerator gegen Erde angelegt. Eine Messung des dann fließenden Stromes führt über das Ohmsche Gesetz zur Ermittlung des Isolationswiderstandes. Wer sich im Detail für diese Messungen interessiert, sei auf diesen Artikel hier im Blog verwiesen. Nach der international gültigen Norm DIN EN62446-1 darf der Isolationswert eines Modulstranges niemals unter 1MOhm liegen.
Nun beobachten wir seit einiger Zeit einen Serienfehler an Solarmodulen, der mit einem Versagen der Rückseitenfolien einhergeht. Die Folge der Fehler in betroffenen PV-Anlagen sind zunehmende Ausfallzeiten, da die Wechselrichter bei zu niedrigen Isolationswerten die Anlage morgens nicht ans Netz nehmen. Im Endstadium des Fehlers kommt es oft zu einem vollständigen Versagen der Rückseitenfolien und zu einer Zerstörung der Module. Es wurde hier im Blog bereits an zwei Stellen auf das Problem hingewiesen, die beiden Artikel sind nachfolgend verlinkt:
Artikel 1: “Die PV-Branche braucht einen professionellen Umgang mit Problemen”
Artikel 2: “Isolationsfehler an PV-Anlagen systematisch finden”
Bevor ich beschreibe, wie man den verwendeten Folientyp eines Solarmoduls bestimmen kann, möchte ich die drei Ausprägungen des beobachteten Problems nachfolgend noch einmal anhand von 3 typischen Fotos zeigen.
Fehlertyp 1
Im ersten Fall sieht man Risse in der Einbettungsfolie immer in den Zellzwischenräumen. Die Zellverbinder werden in der Folge dieses Fehlers so stark geschädigt, dass es zu extremer Hitzeentwicklung kommen muss, die wiederum die Modulglasscheiben zerstört. In der Folge fallen dann, wie in den Aufnahmen zu sehen, ganze Zellreihen aus den Modulen heraus. Das Phänomen wurde zuerst in Südeuropa beobachtet.
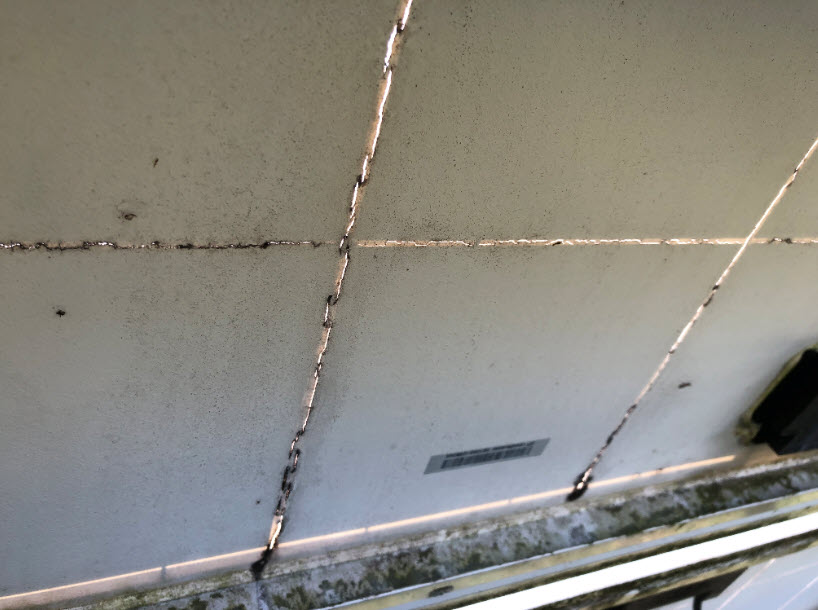
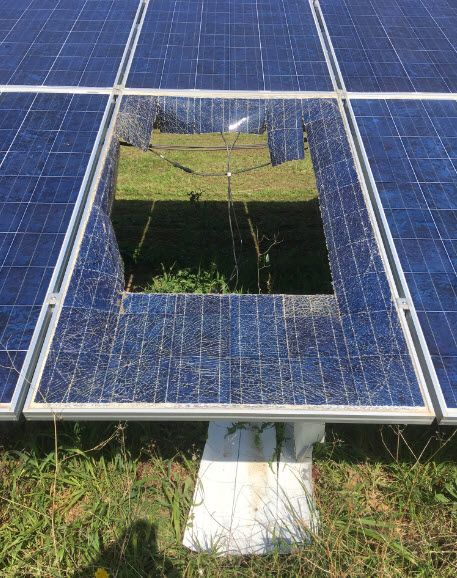
Fehlertyp 2
Im zweiten Fall ist vom rückseitigen Foliensandwich nur die innere Lage betroffen. Das Problem ist auf den ersten Blick leider nicht erkennbar. Leuchtet man jedoch mit einer Taschenlampe durch die Zellzwischenräume, so kann man sehr schön winzige Risse in der Rückseitenfolie erkennen.
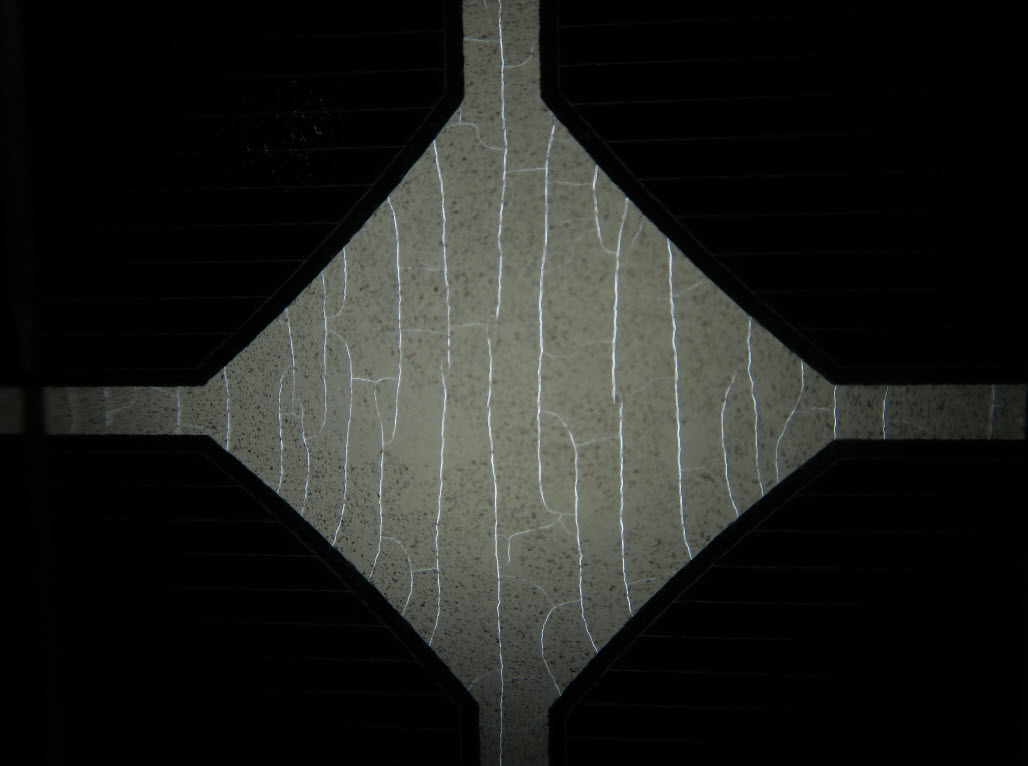
Fehlertyp 3
Im dritten Fall erkennt man über den rückseitigen Zellkontakten Risse in der Folie. In diesem Fall war in den von uns überprüften Anlagen immer auch eine sogenannte Auskreidung (Chalking) festzustellen.
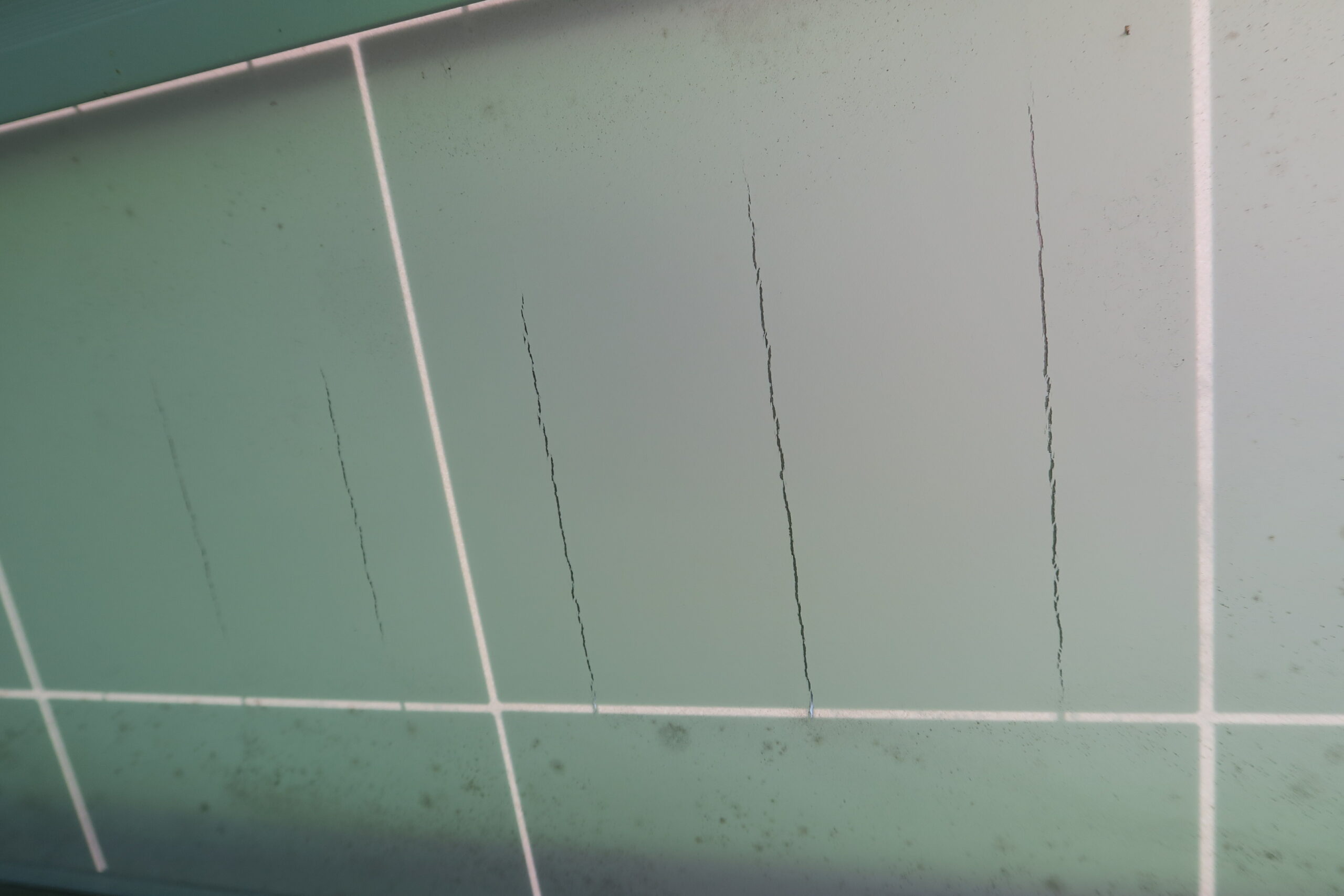
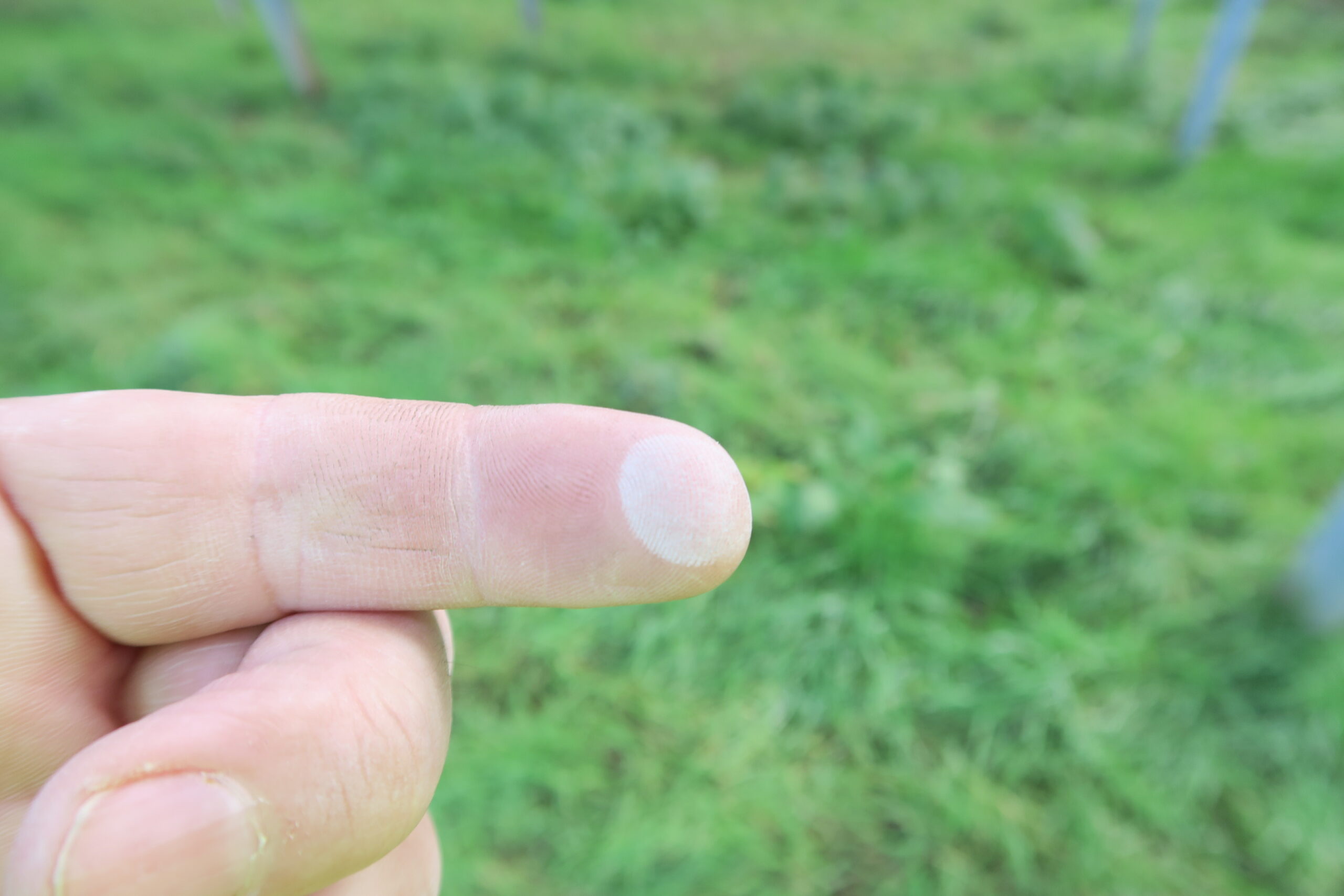
Kann man den Folientyp identifizieren ?
Der Betreiber einer vom oben beschriebenen Problem betroffenen Anlage hat uns mit der Fragestellung konfrontiert, ob es möglich sei, die Folientypen, die das Problem verursachen zu identifizieren, um frühzeitig reagieren zu können. Hintergrund war eine weitere PV-Anlage des gleichen Betreibers, bei der das Problem optisch noch nicht in Erscheinung getreten war. Es sollte also geklärt werden, ob auch in dem zweiten Park mit einem Versagen der Folien gerechnet werden müsste.
Da ich mich mit den Einbettungsfolien bis dato nie näher beschäfftigt hatte, war das für mich Neuland und ich musste mir zunächst einen Überblick verschaffen, welche Untersuchungsmethoden hier möglich sind. Eine Recherche ergab, dass das Labor des ZSW in Stuttgart dazu in der Lage ist, die Rückseitenfolien der Solarmodule zu bestimmen. Zu diesem Zweck mussten Module demontiert und ins Labor gebracht werden. Die Untersuchungen sind nicht zerstörungsfrei. Es werden zum Zweck der Untersuchung Teile aus dem Modul herausgeschnitten, um sie anschließend mit der sogenannten FTIR Methode zu analysieren. FTIR steht hierbei für Fourier-Transform-Infrared-Spectroscopy. Wer sich näher für das Verfahren interessiert, kann hier weiterlesen. Vereinfacht beschrieben wird bei den Spektroskopieverfahren die Wechselwirkung von Nahinfrarotstrahlung mit den Molekülen der Einbettungsfolien genutzt, um diese identifizieren zu können. Jedes Molekül absorbiert eine oder mehrere Wellenlängen der Strahlung, so dass bei Durchstrahlen des Materials ein typischer “Fingerabdruck” des Materials entsteht, der wiederum Rückschlüsse auf dessen Zusammensetzung zulässt. Bei Folien mit mehreren Schichten, muss zur Bestimmung jeder einzelnen Schicht allerdings Schicht für Schicht freigelegt und einzeln untersucht werden. Im Labor lässt sich so etwas realisieren.
Im Ergebnis konnte in unserem praktischen Fall festgestellt werden, dass die Folien aus dem zweiten Park eine andere Materialzusammensetzung aufwiesen, als die fehlerhaften Folien und dass es nicht zu erwarten war, dass diese ebenfalls in gleichem Maße zur Rissbildung neigen würden.
Muss man immer ins Labor ?
Angeregt durch eine sogenannte LowCost IR Spektroskopie Methode, auf die ich vor einigen Jahren einmal aufmerksam wurde, kam mir die Idee zu einer weiteren Recherche nach tragbaren Lösungen, die man eventuell auch im Solarpark einsetzen könnte, ohne dass man dafür die Module ausbauen müsste. Letztlich geht es uns in der Solarbranche ja nicht in erster Linie darum die Folienmaterialien mit einer hohen Genauigkeit zu bestimmen, sondern vielmehr darum, fehlerhafte Folien zu erkennen und von fehlerfreien Folien unterscheiden zu können. Hätte man eine mobile zerstörungsfreie Analysemethode, so könnte man im Laufe der Zeit eine Datenbank aufbauen.
Angeregt durch diesen Gedanken haben wir schließlich Kontakt zu Analyticon aufgenommen, einer Firma, die mobile Infrarotspektroskopie-Geräte vertreibt. Ein Mitarbeiter hat uns besucht und an den zahlreichen Solarmodulen , die sich in unserem Labor als Testobjekte mittlerweile angesammelt haben, wurde versucht herauszufinden, ob sich die gewonnenen Spektren der Einbettungsfolien unterscheiden ließen. Hier ein Beispiel eines solchen Gerätes.
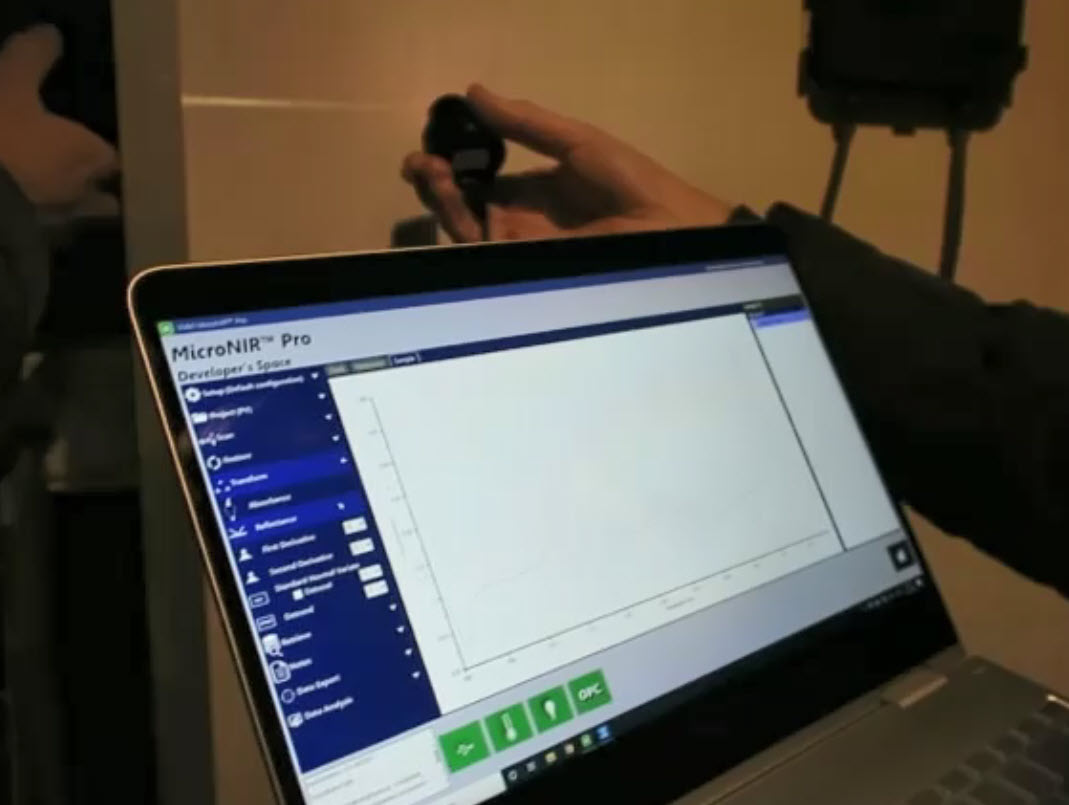
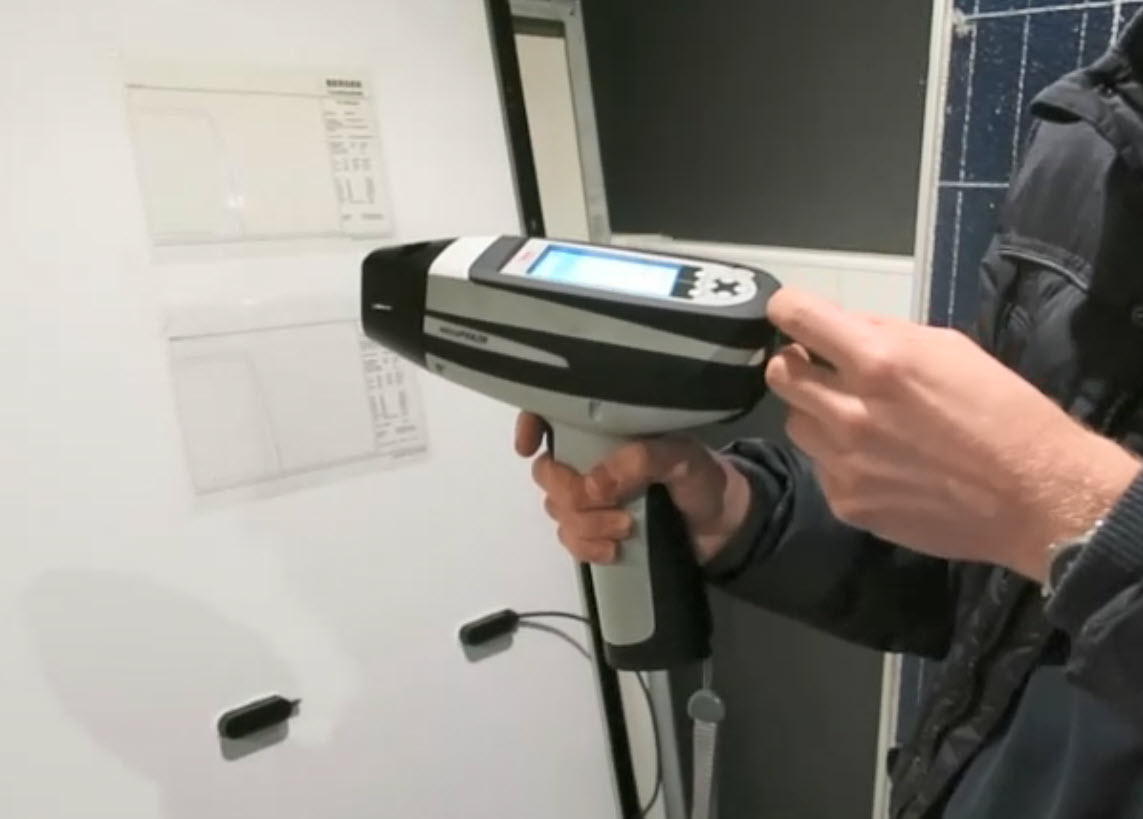
Das Ergebnis war, dass man die Spektren unterscheiden kann, dass man allerdings zur Interpretation der Ergebnisse zusätzliches Know How benötigt, um die jeweiligen Spektren einem spezifischen Einbettungsmaterial zuordnen zu können. Die Kosten für die Geräte lagen alle in einer Kategorie jenseits der 20.000.-€. Es würde demnach sowohl Zeit als auch das notwendige Geld benötigt, um diesen Ansatz weiter zu verfolgen.
Zweiter Versuch
Ein paar Wochen später kamen nochmal zwei junge Männer einer anderen Firma zu uns zu Besuch, auf die wir ebenfalls durch eine Internetrecherche aufmerksam geworden waren. Es handelte sich um die Firma Trinamix aus Ludwigshafen, einer “Startup” Ausgründung der dort ansässigen BASF. Im Gegensatz zur ersten Laborsession hatten die beiden Herrn nur ein kleines Gerät dabei und haben nur wenige Proben von Solarmodulen genommen. Dazu wurde lediglich das kleine Handgerät auf die Rückseite der Module gehalten und ein Knopf gedrückt. Kurz später erschien ein Messergebnis auf einer Handyapp. Man interessierte sich in erster Linie dafür, wie die Anwendung der gewünschten Technik denn genau aussehen sollte, wie groß der Markt dafür in etwa eingeschätzt würde und wofür man typischerweise eine Information über den Zustand und die Beschaffenheit von Rückseitenfolien von Solarmodulen benötigte. Ich habe die Herrn daraufhin mit vielen Informationen zur Photovoltaik und insbesondere zu der aktuellen Problematik im Zusammenhang mit Rückseitenfolien versorgt. Die beiden gingen wieder mit dem Hinweis “sie würden mal drüber nachdenken ob das Thema für sie interessant wäre” … Danach war erstmal Funkstille.
Ein neues Werkzeug zur Untersuchung von Solarmodulen ist geboren
Plötzlich und völlig unerwartet klingelte etwa ein halbes Jahr später unser Telefon und ein Mitarbeiter der vorgenannten Firma war am Apparat. Stolz wurde mir verkündet, das Gerät sei jetzt fertig, die entsprechende APP sei entwickelt und man wolle mir das Gerät gerne einmal bei uns im Büro vorstellen. Ich war offen gestanden sehr überrascht, dass man sich dem Thema ohne weitere Ankündigungen angenommen hatte und freute mich auf einen erneuten Besuch von Trinamix. Bei dem Termin wurde mir die neue Lösung vorgestellt und ich war sehr beeindruckt. Man hatte sich mittlerweile mit dem Österreichischen Forschungsinstitut für Chemie und Technologie (OFI) und dem Polymer Competence Center Leoben GmbH (PCCL) zusammengetan und gemeinsam eine Datenbank der typischerweise in der PV-Branche eingesetzten Rückseitenfolien erstellt. Das kleine tragbare Gerät funktioniert nach dem Prinzip der Transflektrometrie. Das Gerät sendet eine Strahlung im Bereich zwischen 1400nm und 2400nm, also im unsichtbaren Infrarotbereich durch die Rückseitenfolie der Solarmodule. Die Strahlung wird dann von den Solarzellen reflektiert und vom Gerät wieder empfangen. Die reflektierte Strahlung wird spektral aufgelöst und mit der ursprünglichen Strahlung verglichen, um festzustellen, welche Wellenlängen des Spektrums vom Material der Rückseitenfolien absorbiert wurden. Diese Wellenlängen sind, wie oben erwähnt, materialspezifisch und geben einen eindeutigen “Fingerabdruck” des verwendeten Materials. Die Daten werden vom Gerät anschließend zu einer Internetdatenbank gesendet und dort mit bekannten Materialproben abgeglichen. Über diese Zuordnung können dann bekannte Materialien eindeutig identifiziert- und in einer Smartphone-APP unmittelbar nach der Messung angezeigt werden. Ohne aufwändige Laboruntersuchungen hat man damit dann direkt eine Aussage über das verwendete Material der jeweils untersuchten Rückseitenfolie. Als kleine Zusatzinformation ermittelt das Messverfahren auch noch das Einbettungsmaterial, welches wie oben bereits erwähnt, in den meisten Fällen EVA sein dürfte. Die nachfolgend gezeigten Materialien bzw. Materialkombinationen können bereits erkannt werden.
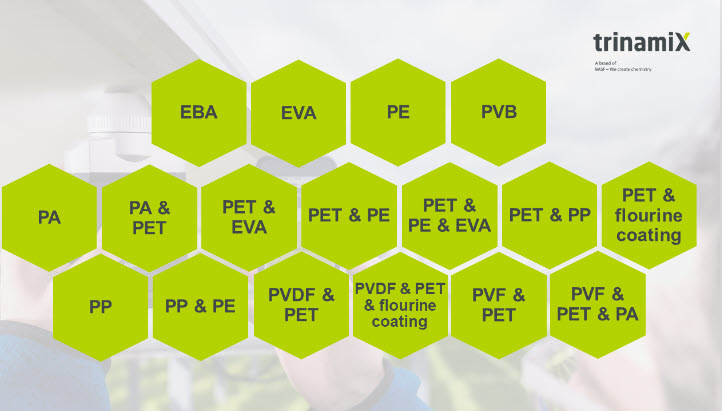
Der Praxistest
Wir haben das Gerät mittlerweile in unserem Werkzeugkasten zur Untersuchung von PV-Anlagen integriert und bereits erste Praxistests damit durchgeführt. Vom Handling her ist das Gerät gut zu bedienen. Man misst jedes Modul in zwei Stufen. Zuerst die Vorderseite und dann die Rückseite. Anschließend wird unmittelbar das Messergebnis angezeigt. Auf Wunsch kann man vor der Messung noch den Modultyp und sonstige Informationen eingeben, die dann automatisch in die Datenbank mit den Messergebnissen wandern. Bei der anschließenden Auswertung im Büro kann man die Messdaten am PC weiterverarbeiten und sich bei Bedarf alle Spektren in Form einer Exceldatei herunterladen. Wer sich mit der Chemie der Folien gut auskennt, kann aus diesen Rohdaten sicherlich noch weitere wertvolle Informationen gewinnen. Ich habe mittlerweile ca. 25 verschiedene Modultypen damit gemessen und nur in wenigen Ausnahmen lieferte das Gerät bisher kein Ergebnis. Diese Ausnahmen waren zwei schwarze Solarmodule und ein uraltes Kyocera Minimodul. Bei den schwarzen Modulen wurde mir erklärt, dass der Ruß, der den Folien zur Schwarzfärbung beigegeben wurde, auch im IR Bereich intransparent ist, so dass die Spektroskopiemethode hier prinzipiell nicht funktioniert. Bei dem uralten Modul wurde ganz offenbar noch ein Folientyp verwendet, der bisher noch nicht seinen Weg in die Datenbank gefunden hat. Bei modernen Glas-Glas Modulen wird übrigens nur der Typ des Einbettungsmaterials (EVA) angezeigt. Da die Datenbasis ständig erweitert wird, kann man davon ausgehen, dass die meisten gängigen Folientypen mit dem System erkannt werden können. Von den oben zu sehenden Fehlerbildern haben wir 2 Module im Labor gehabt und konnten den Folientyp bereits zuordnen. Es handelt sich dabei um PA Folien (PA steht für Polyamide) und um PET & Fuorine-Coating. Wir werden in Zukunft immer, wenn wir zu einer PV-Anlage kommen, routinemäßig mal, zusätzlich zu allen anderen Daten, auch den Typ der Rückseitenfolien aufnehmen und in eine Datenbank ablegen. Die Solarbranche hat allem Anschein nach ein weiteres hilfreiches Werkzeug bekommen, um eine zusätzliche Information über die Solarmodule zu bekommen, die uns bei der Diagnose von Fehlern unterstützen kann.
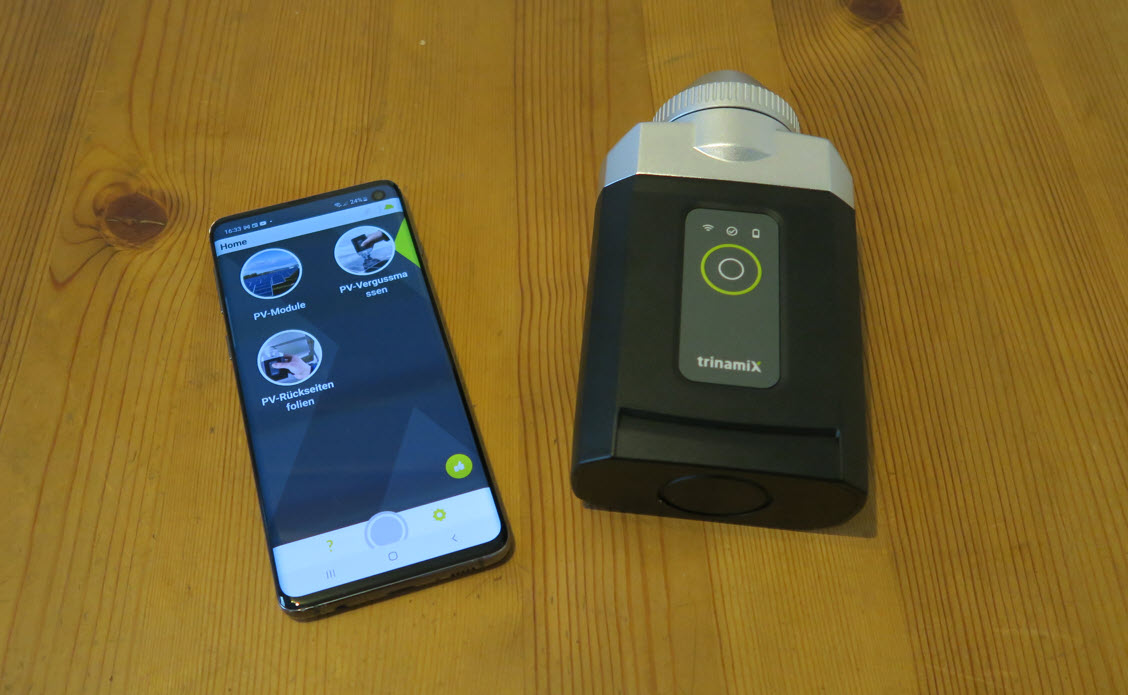
Update 15.11.2022: Ein erster Hersteller reagiert proaktiv auf das Problem und informiert seine Kunden.
Update 19.11.2022: Eine Reparaturlösung von DuPont. (Ich habe damit bisher keine Erfahrungen)
Hallo Matthias, das hört sich gut an. Wir haben auch schon einiges ausprobiert, auf der Intersolar hatte ich mit den Gründern geredet, das schien mir auch schon dort vielversprechend. Danke für den tollen Beitrag! Vielleicht sollten wir mal einen Expertenstammtisch zu Thema degradierende Rückseitenfolien gründen 😉
SG, Erik Lohse, ENERPARC AG (früher MBJ Services).
Hallo Herr Diehl,
ja, das Thema wird zunehmend heißer.
Vorab, die DuPont Lösung halte ich für unpraktikabel. 20 MW entsprechen ca 80000 Module, bei damals üblichen 230-240W. Zeitaufwand, Genauigkeit sowie Qualität und die Gewährleistung werden in keinem Verhältnis stehen. Wir haben das ähnlich von chinesischer Herstellerseite vorgeschlagen bekommen. Es gibt da paar Erfahrungen von auf Recycling von PV Modulen spezialisierten Unternehmen, welche das, als in der Praxis nicht durchführbar, bezeichnen. Die ganze
Logistik um das im großen Maßstab durchzuführen ist unglaublich aufwendig. Die Kosten für ein Repowering sind da ähnlich. Mit dann neuen, leistungsstärkeren Modulen auf weniger Fläche. Denn Ab- und Aufbauen muss man ja so oder so.
Ob der kleine PV Anlagen Besitzer davon betroffen ist, dass wäre mal interessant. Momentan sieht man diese Problematik ja nur auf Freiflächenanlagen. Natürlich ist der Check auf dem Dach ungleich schwieriger. Einbußen in der Performance des einzelnen Modules haben wir zumindest nicht per se festgestellt. Im Gegenteil, auch offensichtlich stark betroffene Module haben mit dem PV 1-1 geprüft, 199 MOhm angezeigt. Erst beim kompletten Bruch der Zellen ist das Modul defekt. Ob und inwieweit kleine StringWR den ISO Wert prüfen, weiß ich nicht. Vermutlich sollten sie es tun. Denn das eigentliche Problem ist ja das der Sicherheit. Ketzerisch gesagt kann ich ja den Schwellwert heruntersetzen und den Park für alle zum Begehen verschließen. Und beim eventuellen Einsatz entsprechend quasi unter Spannung arbeiten lassen. Mit allen dafür vorgesehenen Maßnahmen. Rein aus der wirtschaftlichen Betrachtung nicht von der Hand zu weisen. Allerdings werde ich damit nicht erfahren wie schnell meine Module ausfallen. Und somit habe ich das folgende Problem, was ja die Grundlage für eine wirtschaftliche Betrachtung ist, nicht im Griff. Aus unserer Sicht, Erfahrung in einem 2010 erbauten Park, ist dies eine steigende exponentielle Funktion. Und somit sollte jeder Betroffene sich mit geeigneten Maßnahmen beschäftigen, da die Anlagen ja definitiv länger als die ursprünglichen 20 Jahre leben. Auf die Herstellergarantie ist da leider kein Verlass. Das ist zumindest Stand heute klar. Vielleicht auch ein Grund gewisse Dinge nicht komplett nach außen zu verlagern. Naja, das ist wohl ein anderes Thema.
zur Info: “PV 1-1 geprüft, 199 MOhm angezeigt”
Mit dem Benning PV-1-1 kann man Einzelmodule nicht messen. Einzelmodule haben ISO Werte im Gigaohm Bereich (typischerweise 4-10 GOhm). Das liegt deutlich über dem Messbereich des Benning.
Hallo Matthias,
Denkfehler? Module müssen lt. Zertifizierung einen Mindestwert von 40 MOhm/m2 Modulfläche haben. Ich wüsste jetzt nicht, dass wir uns im GOhm-Bereich bewegen. Neue Module haben in der Realität Werte um die 100 MOhm. Dementsprechend wäre jedes Einzelmodul mit dem Benning messbar. Die genannten 199MOhm deuten eher auf einen Handhabungsfehler hin, findet man oft in Messprotokollen von ganzen Modulstrings.
Hallo Wolfgang,
wir haben öfter schon mal ISO Werte von Einzelmodulen die noch in Ordnung waren gemessen. Die Messwerte lagen immer im GigaOhm-Bereich so um die 4 GOhm, gemessen mit einem Keysight U1461A. Wenn Du dann z.B. 22 Module in Reihe schaltest schaltest Du die ISO-Widerstände ja quasi parallel. Es ergibt sich 1/4000MOhm + 1/4000MOhm …. = 1/Rges. Bei 22 Modulen in Reihe kommt man damit auf 182 MOhm, einem Wert den man mit dem Benning messen kann. Ich hab’s noch nie geschafft mit einem Benning ein Einzelmodul zu messen. Die 40MOhm*m² kommen aus der IEC 61215. Es heißt nicht 40 MOhm/m², sonst müsste der ISO Wert mit zunehmender Modulfläche ja immer größer werden. Schau mal hier: https://files.sma.de/downloads/Riso-UDE104521.pdf
Hallo Matthias, danke für den Beitrag. Die optischen Aspekte, welche mit dem bloßen Auge erkennbar sind, sind ja bereits länger bekannt. Es stellt sich immer wieder die Frage, insbesondere in Solarparks (bei denen oft unterschiedliche Modulchargen verwendet wurden), ob bei den “nicht auffälligen” Modulen da noch etwas nachkommt, weil selbst die Herstellung mit PA-Folien oft unterschiedlich praktiziert wurde. Das Gerät ist sicherlich interessant, um da vor Ort nähere Auskünfte geben zu können.
Ansonsten ist das eine Never-Ending-Story. Viele Reklamationsabwicklungen dauern bis zu 2 Jahre – wenn man Module von einem namhaften Hersteller hat. Selbst wenn der Reklamationsprozess durchgeht, bleibt der Betreiber oft auf erheblichen Kosten sitzen (Demontage, ggf. Haltekonstruktion auf neue Modulformate abändern, Montage, Gerüste, Handling). Bei “Noname-Modulen” kommen die Kosten für neue Module hinzu, weil da beim Hersteller keiner reagiert (reagieren will – oder die Firma nicht mehr am Markt ist).
Interessant zu wissen: Es gibt mittlerweile auch ein 2-instanzliches Urteil, nachdem die Versicherung außen vor ist. Argument: Der Mangel war bereits bei der Auslieferung des Moduls angelegt. Von einigen Versicherern werden aber die Folgeschäden aus dem Mangel erstattet, wie z.B. Module mit korrodierten Leiterbändchen, Glasbruch oder bereits eingetretene Schmorschäden an der Rückseitenfolie.
Schöne Grüße, Wolfgang Schröder (SV-Büro)
Hallo zusammen.
Bei meiner PV-Anlage ca. 30 KW, ca. 13 Jahre alt, habe ich bei der kompletten Anlage den beschriebenen Fehlertyp 1 siehe Bild 1 (Risse in der Rückseitenfolie)
Frage: Hat schon jemand über die Rückseitenfolie eine weitere Folie geklebt um dafür zu sorgen, dass kein Wasser eindringen kann?
Wenn ja, welche Folie haben Sie verwendet und wie ist das Ergebnis.
Vielen Dank schon mal im Voraus
Schauen Sie mal hier: https://www.linkedin.com/posts/sc-refit-gmbh_dupont-tedlar-pv-recue-tape-and-the-sc-refit-activity-6876826474851119104-UJUw/
Ich gebe dafür allerdings keine Empfehlung, da ich das System nicht kenne.
Matthias Diehl
Vielen Dank, gleiche Adresse habe ich auch anderweitig erhalten. Habe mich schon mit der Fa. in Verbindung gesetzt. Schaut auf jeden Fall schon mal professionell aus.
Wünsche einen angenehmen Tag.
Hallo Herr Diehl,
gibt’s denn eine Massnahme von Händlern, diese Folien bereits vor dem Verkauf auf die bereits bekannten Fehler-Folien zu testen?
Man könnte meinen, den Händler würde das weniger interessieren, aber es gibt ja immer solche und solche…
Grüsse
P. Brosche
Die betroffenen Module wurden zwischen 2010 und 2014 verbaut. Heute gibt es diese Folien nicht mehr bei neuen Modulen.